Supply Chain and Logistics
Today’s supply chains have become very complex because of their dependence on global manufacturing and sourcing. Companies derive tremendous competitive advantage by streamlining and improving their supply chains. Product quality, cost-effectiveness, on-schedule delivery, resilience, and risk mitigation are key to better supply chain management.
CSSI provides a complete range of services tailored specifically to the needs of our clients to analyze / develop and improve all functions of the supply chain from initial product design to final product installation and use. Our customers benefit from our over two decades of hands-on management experience as well as a global network of supply chain professionals available to support our clients in all states of the United States as well as 40 other countries. CSSI utilizes innovative systems and processes to more effectively provide its clients with a full range of global services designed to facilitate cost effective supply chain management and technical support services.
Logistics and Warehouse Management Support
Efficient logistics and inventory management is critical to the success of supply chain management. It contributes to its robustness, agility, efficiency and responding to unplanned situations / emergencies.
CSSI's support services for Supply Chain Logistics and Warehouse Management include:
- Logistics planning, coordination
- Transportation planning, coordination
- Network designs
- Optimization of transportation costs
- Asset visibility
- Inventory Management
- Product, equipment tracking
- Inventory monitoring and periodic audits
- Real-time inventory balances
- Plan, Identify and Manage Inventory by Safety stocks, Cycle stocks, Transit stocks, Reorder stocks
- Maintain history of inventory adjustment, movement and receipt.
- Materials Requirement Planning (MRP)
- Technology insertion
- Asset visibility
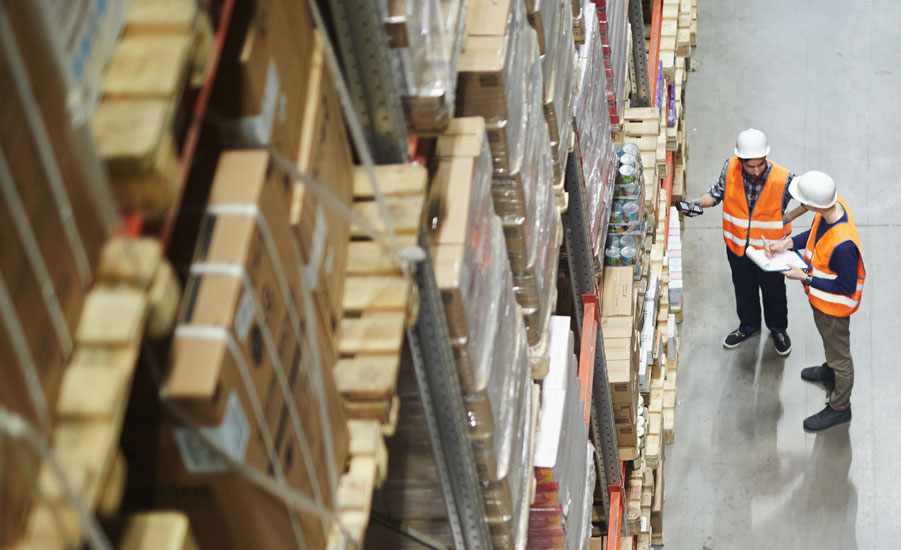
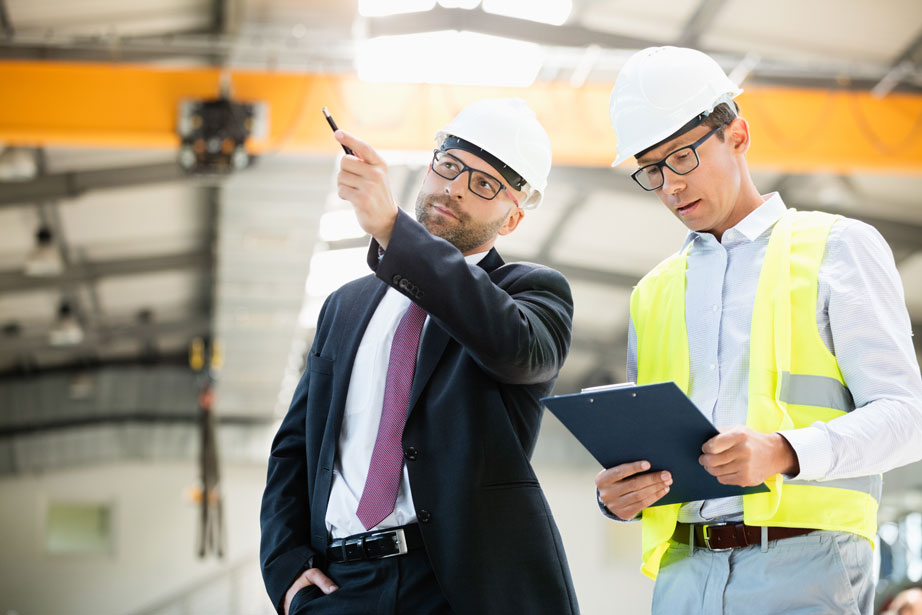
Quality Assurance & Quality Control
CSSI's Quality Assurance and Quality Control (QA/QC) support services aim to assist our customers in ensuring conformance of product, services, processes to requirements throughout the supply chain, via effective Quality Assurance and Quality Control processes, techniques, systems, and policies.
Our support services for Supply Chain QA/QC include:
- Development and implementation of Quality Management Systems (QMS)
- Design and development of Quality procedures, processes, manuals, documentation
- Worldwide Auditing Support services of supplier and subtier supplier compliance with quality, regulatory, standards, and other requirements
- Worldwide Expediting and Delivery Assurance support services
- Resident and on-site representation for Quality Assurance activities
- Nonconformance control and management, Development and control of corrective action plans
- Root Cause Analysis (RCA) to identify, understand, and correct and prevent the recurrence of nonconformance
- Review and development of Production Part Approval Process (PPAP) and Advanced Product Quality Planning (APQP)
- Implementation of Qualified Supplier Certification Programs for self-release of product/material
- Supplier Development, Process Improvements, Implementation of Best Practices
Worldwide Expediting Support
CSSI's Worldwide Expediting Support services cost-effectively assist our customers in monitoring supplier compliance with production, project, and delivery schedules and quality requirements via a global network of expediting professionals with experience in expediting, procurement, manufacturing, QA/QC, material, and production control, ready to support our customers' supply chain and expediting requirements, on-site, in over 40 countries worldwide.
Our support services for Worldwide Expediting Support include:
- Provide an on-site interface between the customer and supplier for field activities
- Monitor and report on supplier program status
- Conducting surveys including inventories of material, work progress, equipment/tooling, logistics and shipping, schedule analysis, supplier processes and capabilities
- Identify and resolve problems, acting as the on-site eyes and ears and representative of the customer at supplier sites
- Recommend process improvements and corrective / preventative actions to resolve production bottlenecks
- Develop detailed schedules, milestones, and tracking performance and schedule slippage
- Develop "workaround" schedules to reflect manufacturing or procurement delays / slippage
- Assist in negotiations for work scope changes
- Coordinate collection of all required customer data requirements and reports
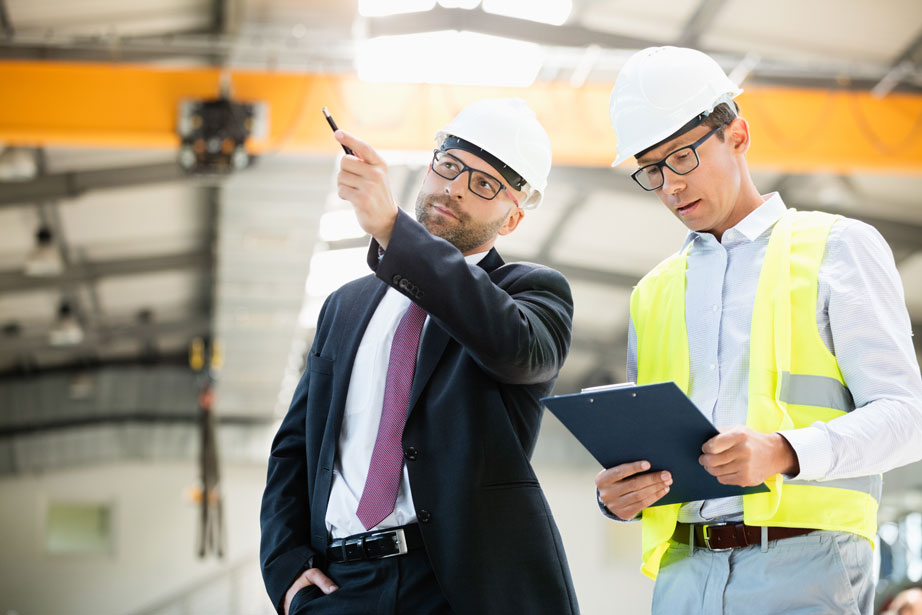
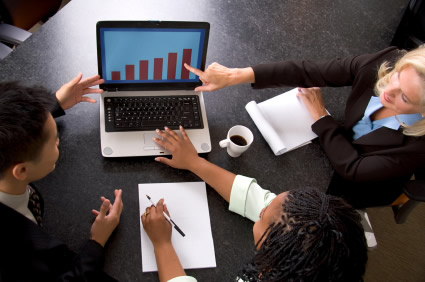
Procurement Support
CSSI's support services for Supply Chain Procurement include:
- Development, review and verfication of requirements, contract documents, specifications development
- Supplier / Supply Chain Risk Assessment
- Procurement Planning and Forecasting
- Supplier capability evaluation, selection and negotiation
- Supplier Relationship Management
- Development of Quality Plans and quality requirements
- Contract Administration and Management
- Pre-award Surveys and Audits
- Development and review of Invitation To Bid (ITB), Request For Proposal (RFP), and Request for Quote (RFQ)
Supplier Development Support
World class supply chain management requires world class suppliers. Supplier development improves the supplier performance and capabilities to meet customer requirements cost-effectively, with high quality (zero defects) and on time delivery. CSSI's Supplier Development support services focus on developing suppliers for self-release of products / material using a structured, process-based supplier development methodology.
CSSI's Supplier Development process includes:
- Project Initiation: CSSI defines the project scope and performs gap analysis of the supplier's current capabilities, quality performance, resources, and procurement system to evaluate conformance with customer requirements and to identify inefficiencies such as long cycle times, inadequate processes, poor quality, lack of control, and training / documentation.
- Mapping and Measurement: CSSI establishes project metrics and metric baselines and analyzes data.
- Process Development & Deployment: CSSI collaborates with the supplier and customer to develop an implementation plan for process development and deployment to improve supplier capability, leveraging our supplier development expertise and a combination of tools, systems, proceses, training, Lean Six Sigma, and Quality and Process Engineering improvements and best practices. CSSI implements supplier management, including improvements to reduce the supplier's cost, responsiveness and quality.
- Monitoring / Process Control: CSSI sets stretch goals and implements continual improvement and sharing of best practices, then conducts audits, surveillance, and quality data review to monitor and measure improvement.
- Closeout: CSSI conducts surveillance, periodic audits, and review of quality data to periodically assess supplier performance. CSSI implements a Qualified Supplier Certification Program to enable supplier self-release, as applicable.
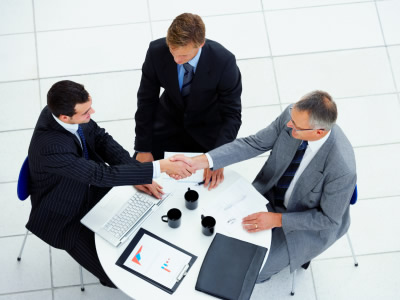